With the rise of new technologies and trends in automotive manufacturing, the automotive production process has become increasingly complex, with components constantly updated and iterative, and production lines frequently switched. This prompts the automotive industry to continuously develop in the direction of customization, flexibilization and intelligence.
Against this background, AUCTECH’s new generation of flexible collaborative robot ACR has become a major booster for the industry with its leading safety, excellent motion performance and superior supple force control features. It has the advantages of simple programming, plug-and-play, rapid deployment , etc. It can cope with a variety of complex processes and working conditions, greatly reduce the transformation costs, enhance the flexibility of the production line, and fully meet the current demand for flexible production.
1. Application: Gluing
In the field of gluing, manual gluing is gradually replaced by robotic gluing because of the problems of poor consistency and uneven amount of glue, which affect the quality of gluing. Considering the automotive industry’s development towards customization, as well as the frequent switching of glue types and adjustments to production lines, safe, flexible and easy-to-switch collaborative robots have become the industry’s new favorite.
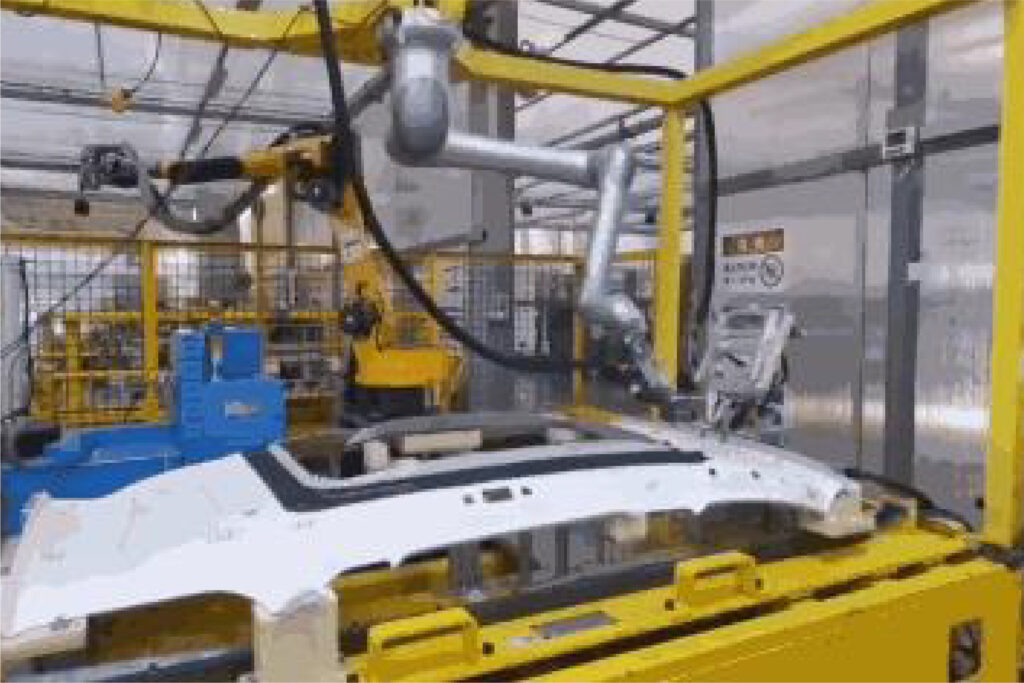
Case: Car Roof Gluing
Solution :
AUCTECH launched the ACR12 collaborative robot arm, with a 1300mm spread, inverted mounting with glue gun and glue supply system, to realize intelligent gluing of car roof, which fully meets the customer’s requirements of high precision and high beat production.
Customer Benefits :
With this robot, the whole gluing operation can be controlled within CT<120s, one robot can replace 2 laborers, and the consistency and uniformity of gluing can be greatly improved.
2. Application:
PolishingThe engine head has a lot of burrs, the manual removal efficiency is low, and easy to produce secondary burrs affecting product quality. At the same time, the harsh grinding environment full of dust and noise is unfriendly for the front-line workers. There is an urgent need to replace the machine with a new one.
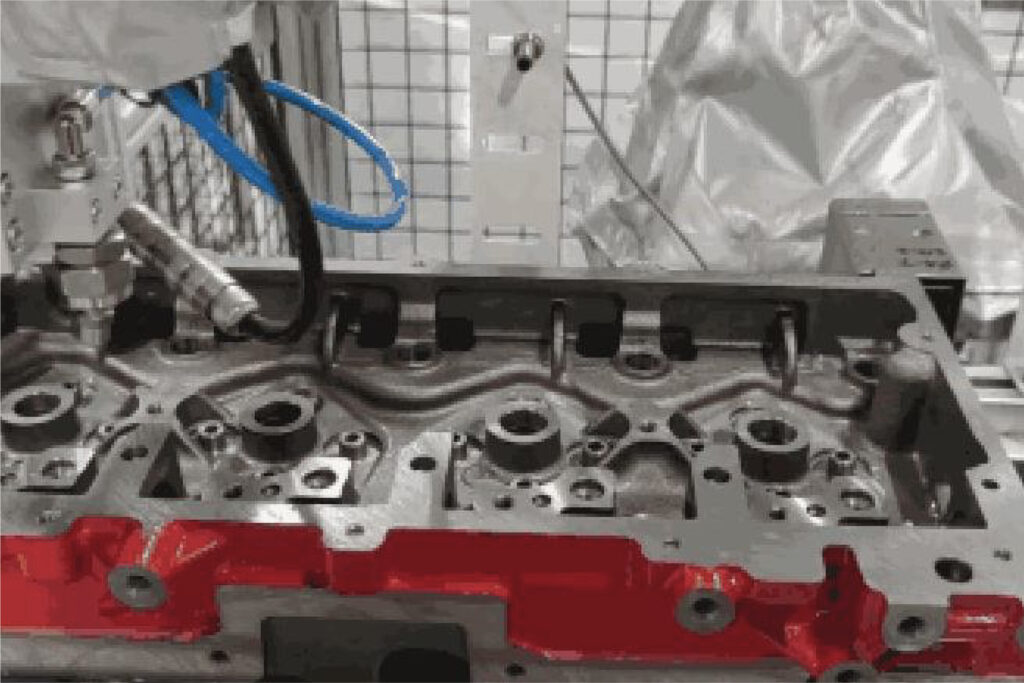
Solution :
Two ACR flexible collaborative robots are used, one for deburring conduit holes, and the other with a floating grinding head to deburr the outer edges of the rocker arm face and the rocker arm face holes.
These robots have a cabinet-less design and extreme safety features for quick setup and deployment without the need for safety fencing.
They are equipped with high-precision force control and proprietary grinding process packages that can be adapted to multiple engine models at the same time. And deburring paths are automatically generated, eliminating the need for manual instruction and simplifying operations.
Customer Benefits :
The use of these robots saves 2 laborers, increases production capacity by 100%, achieves a pass rate of over 99.5%, saves 30% of sanding consumables, and dramatically improves product quality and consistency.
3. Application: Assembling
Traditional manual assembly operations are labor-intensive and have poor production consistency. Many companies urgently need to replace people with machines. However, traditional industrial robots need to be equipped with fences and have a large space requirement, which is not suitable for some compact layout scenarios. Therefore, more and more companies are choosing the rapidly deployable, easy-to -operate collaborative robots.
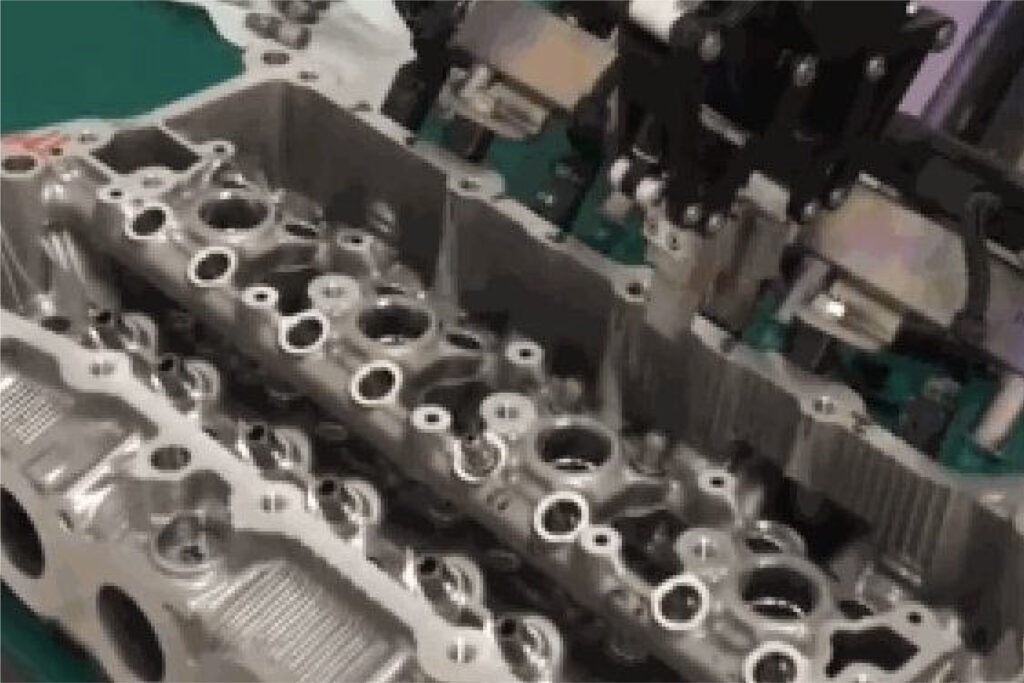
Case: Gap adjuster assembly
Solution :
AUCTECH’s new-generation flexible collaborative robot ACR is used to assemble the clamping regulator. During the assembly process, it detects the force on the regulator in real time, and completes the assembly process stably and reliably with a gap of less than 0.03mm on one side.
Customer Benefits :
It improves the automation level of the production line of the enterprise, helps the enterprise to reduce the labor cost by 35%, and increase the product compliance rate by 15%.
4. Application: Screws Locking
Screws locking work is a boring, repetitive action which is easy to make workers fatigue, thus affecting product quality and production efficiency. Man-machine cooperation is needed for many enterprise, collaborative robots have the convenience of installation and deployment as well as man-machine cooperation security advantages, which can rapidly improve the production efficiency.
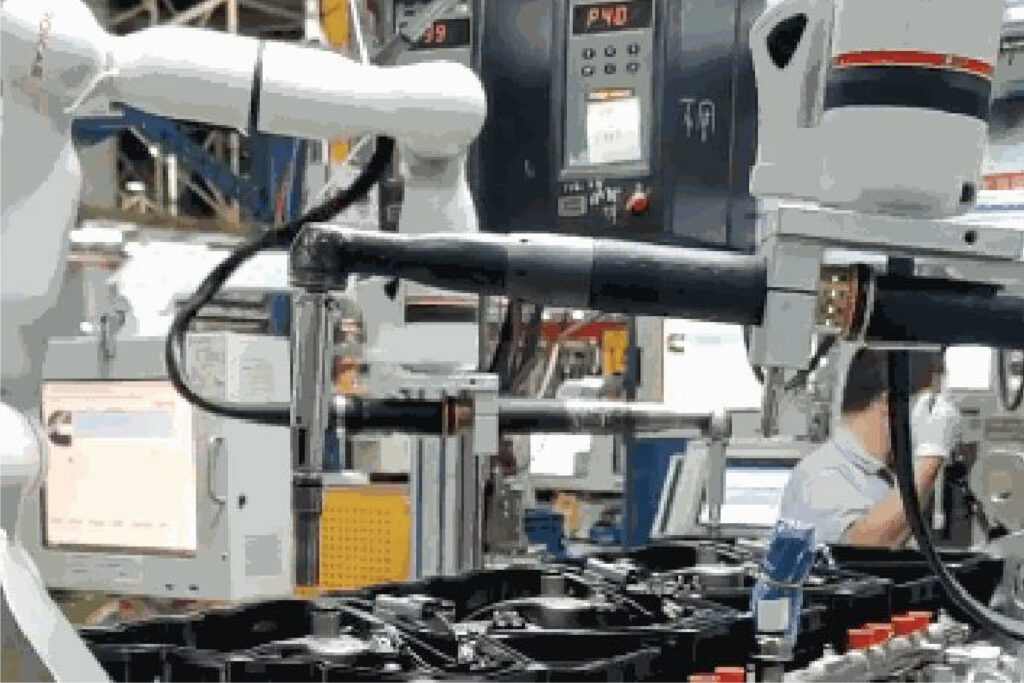
Case engine bolt tightening
Solution :
AUCTECH Robotics’ AER collaborative robot with a tightening gun to tighten bolts sequentially, achieving a torque range of 70Nm, adapting to a variety of products and bolt specifications; repetitive positioning accuracy of less than ±0.03mm to ensure consistency of the screwing; the leading design of the no-control cabinet so that it occupied less than 1 square meter, greatly reducing production line space and transformation costs; convenient and easy to install and deploy. Sensitive collision detection combined with a number of safety features to perfectly solve the user’s safety needs, and truly realize humanmachine collaboration.
Customer Benefits :
Helping a Tier1 customer to complete the production line automation upgrade, production efficiency increased by 30%, and the return on investment (ROI) cycle is less than one year.
5. Application: Automatic Charging
AUCTECH Robotics With the explosive growth of electric vehicles and the increasing maturity of autonomous driving technology, automatic charging will become a standard feature in the electric vehicle ecosystem.
Therefore, how to quickly and conveniently replenish power for electric vehicles has become a new issue for many charging pile enterprises.
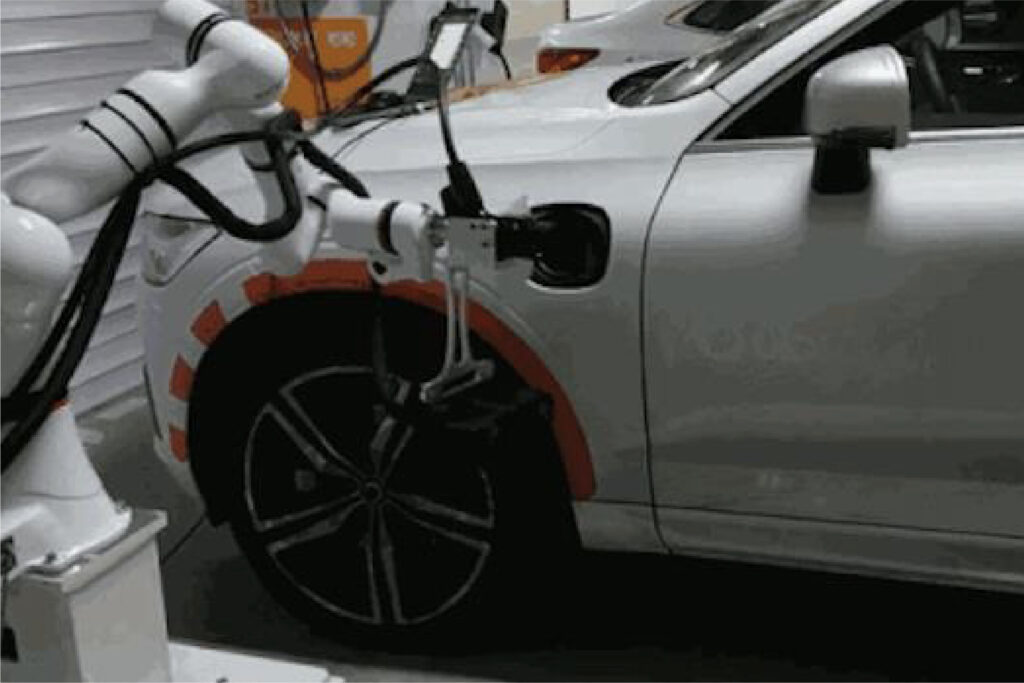
Case Study Unmanned Charging for Electric Vehicles
Solution :
AUCTECH Robotics’ automatic charging robot can realize unmanned automatic charging. Through the navigation system and vision system equipped with the robot, it can accurately identify the position of the vehicle and the charging interface, and realize accurate docking and automatic charging. With autonomous movement and collision detection, the robot can safely move between charging piles to charge multiple vehicles.
Customer Benefits :
It improves the efficiency and charging speed of charging piles, providing users with a more convenient and faster charging experience. At the same time, it reduces the labor intensity of the staff and lowers the labor cost.
The above are the application cases of AUCTECH Robotics in the field of assembly and charging. Through innovative collaborative robotics, it helps enterprises realize automation and intelligence of production, improve production efficiency and product quality, reduce labor costs, and create greater economic benefits for enterprises.
In conclusion, AUCTECH’s new generation of flexible collaborative robots, ACR, is playing a huge role in the automotive parts industry. As the industry moves toward customization, flexibility and intelligence, these robots will surely continue to drive breakthroughs and progress in the industry.